I am by no means an expert, I just enjoy working on my own cars. Following this guide is done entirely at the reader's own risk.
Symptoms for the failure of this bush are described here.
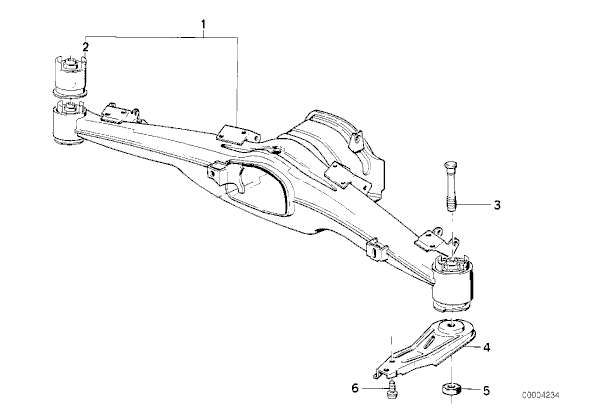
Item number 2 is the bush, rather misleading shown above the subframe as it actually assembles into the bottom of the subframe housing. It is about the size of a Coke can. Its anatomy, very simply, is an outer steel cylinder and an inner steel pillar, which is bonded to the outer by means of solid rubber. This rubber connection is what isolates the vibrations of the road/subframe assembly from the vehicle. The outer cylinder is also coated in the same rubber.
The fit into the subframe housing is pretty tight, although not a press fit, as in metal on metal, but tight enough to warrant the need for some sort of tool to pull/push it in and out. Do not even bother starting this job without a tool like this at hand.
1. With the car still on the ground, using a 22mm socket and breaker bar, (it will be tight!) slacken the nut (item 5 in diagram) that passes through the bush under the car first, both sides. This is simply because this nut will be pretty tight and it is better to do this with the car safely on the ground, rather than heaving it about with the car on axle stands.
I had to extend my breaker bar with a length of steel pipe to get enough leverage on it.
2. Safely lift the rear of the car (both wheels) off the ground and SECURELY AND SAFELY put it on axle stands. NEVER work under a car that is only supported by a jack. Jacks can fail!
NOTE: Do not put the axle stands under any of the rear running gear as this is all connected to the rear subframe and will therefore prevent you from lowering the subframe to do any of the work. I supported my car under the sill down the side of the car, using some 2x2 wood to spread the load.
Place a jack under the rear subframe, just to hold it up when you take the bush out. It could be left to just flop down, still supported by the other side, but I found it useful to have a jack under it to be able to wind it up and down.
3. Remove the nut plus the two fixings screws (item 6) that hold the support plate on (item 4) and put to one side.
Put the nut back on loosely so the pin (item 3) is just about to protrude out the nut. This needs to be belted with a hammer, so the nut is just to protect the end of the pin. The reason for this is because the pin has a knurled pattern under its head which locks it into position in its bore, which is accessed through the inside of the car under the rear seat.
Remove the rear seat (it just pops out if you lift it from the front edge hard). Peel back the sound deadening material from the area near the bush. The actual bore that the pin is in was hidden under a small square piece of sticky-back foam, I guess to prevent ingress of moisture.
5. With a lump hammer, repeatedly hit the nut and pin from underneath to drive the pin out of the bore. So you are hitting it up into the car. It took quite a lot of heavy blows so don't give up! Just be wary not to damage the end of the pin, although it wouldn't be the end of the world if you had to get a new one.
![]() |
Pin and Nut |
6. Now the subframe on this side is free from the vehicle, and if you lower the jack, the whole subframe will sag down. This opens up the vital gap between the top of the bush and the underside of the vehicle for you to get the top piece of the tool in place.
![]() |
Old Bush in Car |
Note, this bush is protruding out of the housing already by about 25mm. This could be either due to slippage, but I suspect more likely it has been replaced before and incorrectly (or rather incompletely) installed. More on the possible reasons for this later.
I put the top disk in place on top of the bush, fed the threaded bar up through the bush and plate, then added two or three washers and finally a nut.
![]() |
Tool in place |
I also added a G-clamp across the fork to prevent the fork from splaying open and popping off the edge of the housing.
Then I put about three or four washer on plus the nut. Add a load of grease between each washer. This really helps when winding the nut against the tool with the resistance of the tight bush. I have even seen some guides recommend using a thrust washer, which would be nice, but unless you already have one I wouldn't bother buying one.
![]() |
Tool in Place with G-Clamp |
![]() |
Old Bush Out with Tool |
I was relieved that this seemed to happen quite easily. Not very easily, it still required a lot of effort, but not to the extent where I thought it wasn't going to work. So just gradually, it worked its way out until, pop, it was out.
![]() |
Bush Failure |
This would have let the rear subframe (and hence rear wheels/diff) slide up and down vertically when putting power on and off. Hence the clunking and sunken appearance of the car. Its always nice to see something properly failed so as to remove any doubt.
My tool did take a bit of a pounding, the bridge piece bending a bit and the top disk piece dished too. So I will thicken these up if I am to do the job again.
8. Fitting the new bush sounds simple, just pushing the new one into the housing, but it wasn't quite that straight forward.
To fit the bush, I dismantled my tool, so I could use the bridge part of the fork across the top of the housing and the disk against the bottom of the bush, then use the threaded bar and nuts to wind it in.
The problem I soon realised was that the bush needs to protrude past the top of the housing, so using something straddling the top of the housing wouldn't work as it would just wind in until it hit that and not be able to continue through the housing to its final location.
![]() |
Installing New Bush (with wood) |
So to get around this, I decided to feed my threaded bar down through the hole from the inside of the car (where the original pin goes) with nuts and washers to stop it. This passed right down through the bush. I then put the bridge piece under the bush to push against the bush with.
There was one more complication where if I started winding this up, the gap between bush and vehicle would close up until the bush was against the vehicle. This would happen, lifting the subframe way before the bush would actually start going into the housing, as the housing needs to be held rigidly to allow the bush to press in.
So I simply wedged a block of wood between the subframe and vehicle to hold it off to allow me to press the bush in and through the housing.
You can just see the wood top right in this image.
9. Apply and keep applying lots of soapy water to the sides of the bush to help it slip in. Do not use neat washing up liquid, but dilute it just like you were doing the washing up. Neat washing up liquid or oil would not dry up and the bush could risk slipping back out in use.
Then just keep gradually winding the nut up. Slowly the bush will sink into the housing until it is about a fingertip width between the lip of the bush and the underside of the housing.
10. Done! Refit the pin (drop it into the hole and knock it in with a drift and hammer a bit), refit the support plate, with screws and nut. Torque up the nut. This will go stiff for a while as it draws the knurled pin back into place before finally going tight.
11. Repeat for the other side.
No comments:
Post a Comment